Complete Guide to OPC Cement – Everything You Need to Know
February 28, 2024
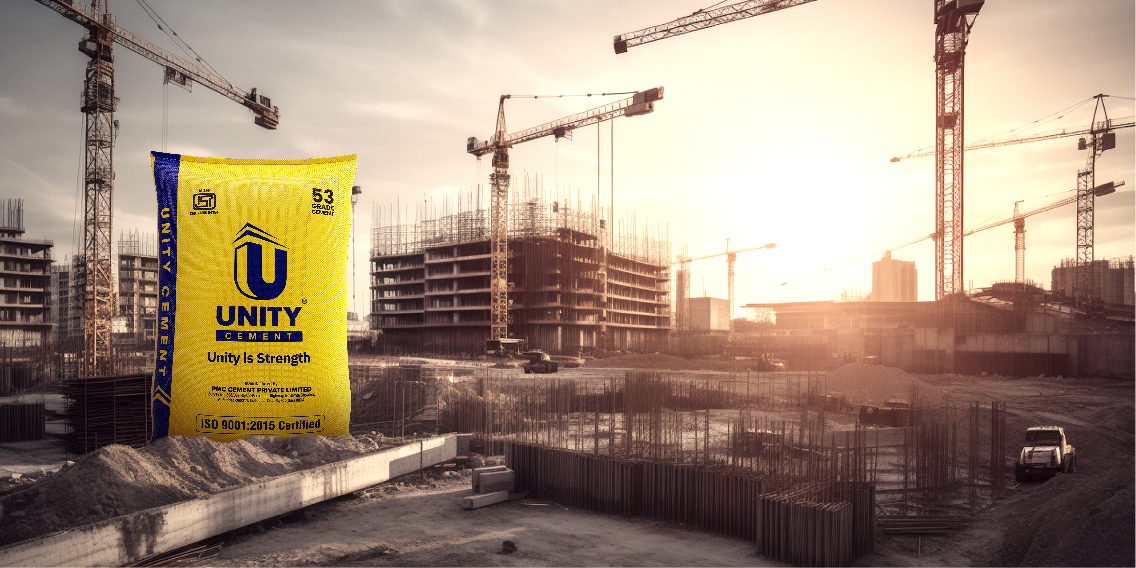
Introduction
There are many types of cement and Ordinary Portland Cement (OPC) is one of them. When it comes to constructing robust and durable structures, the choice of cement plays a pivotal role. Ordinary Portland Cement (OPC) stands as a cornerstone in the world of construction materials, offering unparalleled strength and versatility. In this comprehensive guide, we delve into the depths of OPC cement, exploring its meaning, composition, types, applications, advantages, and industry trends.
What is OPC Cement?
Ordinary Portland Cement, commonly known as OPC cement, is a widely used construction material known for its binding properties. It’s the foundational element in various construction projects, providing the necessary strength and durability.
OPC cement is the backbone of the construction industry. It serves as the primary ingredient in concrete, mortar, and other construction materials. Its ability to harden and bind makes it indispensable for creating structures ranging from residential buildings to massive infrastructure projects.
Raw material used in OPC Cement
The quality and performance of Ordinary Portland Cement (OPC) are intricately tied to the selection and composition of its raw materials. Let’s delve into the essential components that lay the foundation for this indispensable construction material.
1. Limestone
Role
Limestone serves as the primary source of calcium in OPC cement.
Function
It undergoes chemical reactions during the manufacturing process, contributing to the cement’s strength and durability.
Quality
High-purity limestone is preferred, as impurities can impact the final product’s characteristics.
2. Clay or Shale
Role
Clay or shale provides the necessary silica, alumina, and iron oxide.
Function
These elements, when combined, contribute to the cement’s hydraulic properties and enhance its performance.
Variations
Different types of clay and shale are used based on their availability and chemical composition.
3. Iron Ore
Role
Iron ore adds iron oxide to the mix.
Function
This imparts color to the cement and influences its setting and hardening properties.
Control
The amount of iron ore must be controlled to prevent undesirable effects on the final product.
4. Gypsum
Role
Gypsum is added in small quantities.
Function
It regulates the setting time of OPC cement and prevents flash setting, ensuring workability during construction.
Control
Precise control of gypsum content is crucial to achieving the desired setting characteristics.
Understanding the significance of each raw material is fundamental to producing OPC cement with consistent quality. The selection process involves thorough testing and analysis to ensure that the raw materials meet stringent standards. Variations in raw material composition can impact the cement’s performance, making it imperative to maintain strict quality control throughout the manufacturing process.
Manufacturing Process of OPC Cement
The transformation of raw materials into Ordinary Portland Cement (OPC) is a sophisticated process that involves precise steps, high temperatures, and chemical reactions. Let’s unravel the intricate manufacturing journey that brings OPC cement to life.
Step 1: Crushing and Grinding
Raw Meal Formation: Limestone, clay, shale, iron ore, and gypsum are crushed into fine particles.
Homogeneous Blend: The crushed raw materials are then blended to create a homogeneous mixture known as raw meal.
Step 2: High-Temperature Calcination in Kiln
Formation of Clinker: The raw meal undergoes high-temperature calcination in a rotary kiln, reaching temperatures of up to 1450°C (2642°F).
Chemical Reactions: Intense heat triggers chemical reactions, transforming the raw materials into small nodules called clinker. This is the heart of OPC cement.
Step 3: Cooling of Clinker
Stabilizing Temperature: The hot clinker is cooled, stabilizing its temperature before further processing.
Clinker Quality: Proper cooling is crucial for optimizing clinker quality, which directly influences the final cement product.
Step 4: Grinding of Clinker
Clinker to Cement Powder: The cooled clinker is finely ground into a powder using ball mills or vertical roller mills.
Particle Size Control: The grinding process ensures the desired particle size distribution, which is critical for the cement’s performance.
Step 5: Quality Control
Testing and Analysis: Throughout the manufacturing process, rigorous quality control measures are implemented.
Consistency: Consistent testing ensures that the final OPC cement meets established standards for strength, setting time, and other critical properties.
Step 6: Packaging and Distribution
Packing: The final OPC cement is packed into bags or transported in bulk.
Distribution: The cement is ready for distribution to construction sites, where it will play a crucial role in building robust and enduring structures.
Types of OPC Cement
Exploring the different grades and variants of Ordinary Portland Cement (OPC) provides valuable insights into choosing the right type for specific construction requirements. Let’s delve into the characteristics of OPC 33 Grade, OPC 43 Grade, OPC 53 Grade, and special variants like Rapid Hardening OPC.
1. OPC 33 Grade
Characteristics
OPC 33 Grade cement is characterized by its relatively low compressive strength compared to higher grades.
Application
It is commonly used in plastering, finishing works, and non-structural concrete where high strength is not a primary requirement.
2. OPC 43 Grade
Characteristics
OPC 43 Grade cement offers a balanced combination of strength and affordability.
Applications
Suitable for general construction purposes, including residential buildings, commercial structures, and pavements.
3. OPC 53 Grade
Characteristics
OPC 53 Grade cement is known for its high compressive strength and durability.
Applications
Ideal for structural applications where strength and load-bearing capacity are critical, such as bridges, high-rise buildings, and heavy-duty pavements.
Unity Cement stands out by specializing in the production of OPC 53 Grade cement. This grade reflects our commitment to providing top-notch construction materials for projects that demand the highest levels of strength and reliability.
4. Special Variants (e.g., Rapid Hardening OPC)
Characteristics
Special variants of OPC cement, such as Rapid Hardening OPC, are engineered to achieve early strength gain and rapid setting times.
Applications
These variants are favored for time-sensitive projects, repairs, and construction in cold weather conditions where quick setting is advantageous.
Understanding the characteristics and applications of each type of OPC cement allows builders and engineers to select the most suitable grade based on the specific requirements of their construction projects. Whether it’s achieving structural stability, cost-effectiveness, or meeting tight deadlines, the diverse range of OPC cement types offers solutions to a variety of construction challenges.
Advantages of OPC Cement
Ordinary Portland Cement (OPC) stands out as a cornerstone material in the construction industry, offering a multitude of advantages that contribute to its widespread use. Here are the advantages of OPC cement in construction projects:
1. Exceptional Compressive Strength
OPC cement is renowned for its remarkable compressive strength, providing structures with the necessary robustness to withstand heavy loads and external pressures.
2. Versatility in Applications
Its versatility allows OPC cement to be employed in a wide range of construction applications, from residential buildings to massive infrastructure projects.
3. Cost-Effectiveness
OPC cement offers a cost-effective solution without compromising on quality. Its availability and affordability make it a preferred choice for various construction projects.
4. Rapid Setting and Hardening
OPC cement exhibits relatively fast setting and hardening properties, facilitating quicker construction timelines and allowing for earlier use of structures.
5. Ease of Use and Workability
OPC cement provides excellent workability, making it easy to mix, place, and finish during construction activities. This contributes to the efficiency of the construction process.
6. Durability Against Environmental Factors
The durability of OPC cement ensures resilience against environmental factors such as moisture, temperature variations, and chemical exposure. This longevity contributes to the sustainability of structures.
7. Adhesive Properties
OPC cement forms strong adhesive bonds with aggregates, ensuring the structural integrity of concrete. This property is crucial for the overall stability of construction projects.
8. Consistent Quality
Manufacturers adhere to stringent quality control measures, ensuring that OPC cement maintains consistent quality across batches. This consistency is essential for reliable construction outcomes.
9. Proven Track Record
OPC cement has a long and proven track record in the construction industry. Its reliability and effectiveness have been demonstrated in countless successful projects worldwide.
10. Compatibility with Additives
OPC cement can be easily modified and enhanced with various additives to meet specific construction requirements, providing a tailored approach for diverse projects.
11. Wide Availability
OPC cement is widely available in the market, making it accessible to construction professionals and enabling seamless integration into construction projects of all scales.
Uses of OPC Cement
Ordinary Portland Cement (OPC) is a versatile construction material widely employed in various applications across the construction industry. Here are the primary uses of OPC cement:
1. Structural Foundations
OPC cement is extensively used in the creation of foundations for buildings, ensuring stability and strength.
2. Residential Construction
From small homes to large residential complexes, OPC cement is a key component in constructing durable and robust structures.
3. Commercial Buildings
The compressive strength of OPC cement makes it an ideal choice for constructing commercial buildings, providing stability and durability.
4. Infrastructure Projects
Bridges, roads, dams, and other infrastructure projects rely on OPC cement for its ability to withstand external forces and environmental conditions.
5. Precast Concrete Products
OPC cement is used in the production of precast concrete products such as pipes, panels, and blocks, contributing to efficient construction processes.
6. High-Rise Structures
The high compressive strength of OPC cement makes it suitable for constructing tall buildings, ensuring structural integrity under significant loads.
7. Masonry Work
OPC cement is a fundamental component in masonry work, providing the binding agent for bricks and blocks in walls and partitions.
8. Road Construction
In road projects, OPC cement is used in the construction of pavements and structures, contributing to the durability and load-bearing capacity of the roads.
9. Water Retaining Structures
OPC cement is commonly used in the construction of water tanks, reservoirs, and other water-retaining structures due to its durability and resistance to water penetration.
10. Repair and Rehabilitation
OPC cement plays a crucial role in repair and rehabilitation projects, where it is used to strengthen and restore the integrity of existing structures.
11. Specialized Applications
Various specialized OPC cement variants, such as Rapid Hardening OPC, find applications in projects with time-sensitive requirements or specific performance needs.
12. Soil Stabilization
OPC cement is utilized for soil stabilization, enhancing the load-bearing capacity of the soil in construction projects.
13. Decorative Concrete
In decorative applications, OPC cement forms the base for creating various finishes, textures, and designs in concrete surfaces.
The diverse uses of OPC cement showcase its adaptability and reliability, making it a foundational material for construction projects of varying scales and complexities. Its wide-ranging applications contribute to its status as a go-to choice for builders and engineers worldwide.
Conclusion
In wrapping up our journey through Ordinary Portland Cement (OPC), it’s clear that OPC isn’t just a building material – it’s the backbone of durability and strength in construction. With its exceptional properties, Unity Cement’s commitment to excellence, and diverse applications, OPC cement proves its worth in projects of all sizes.
Whether laying foundations, constructing skyscrapers, or adding decorative finishes, OPC cement stands as a reliable ally. It’s not just about building structures; it’s about crafting a sustainable future where strength and resilience go hand in hand. With Unity Cement leading the way, OPC cement becomes more than a material – it becomes the key to constructing a robust and enduring tomorrow.