Concrete Mix Ratio: A Comprehensive Guide by Unity Cement
April 12, 2024
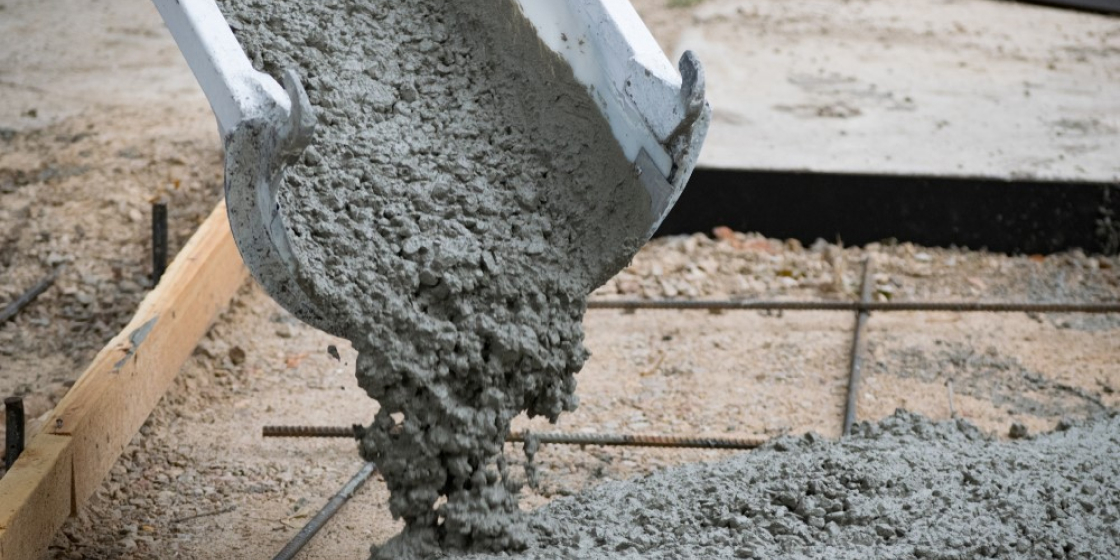
Introduction
The foundation of any solid construction project lies in its concrete mix ratio. It’s not merely a matter of pouring cement, water, and aggregates together; rather, it’s a precise science that determines the strength, durability, and overall quality of the structure. The concrete mix ratio dictates the proportions of each ingredient—cement, aggregates, water, and sometimes additives—necessary to achieve the desired characteristics in the concrete. Whether you’re building a small patio or a towering skyscraper, getting the mix ratio right is crucial for ensuring the structural integrity and longevity of the project.
In this comprehensive guide, we’ll delve deep into the world of concrete mix ratio. We’ll start by understanding the significance of mix ratios and why they matter in construction projects of all scales. Then, we’ll explore the key components of a concrete mix from cement to aggregates, and discuss their roles in determining the final product’s properties. Next, we’ll learn how to determine the right mix ratio for various applications and the importance of testing and quality control measures. By the end of this blog, you’ll have a comprehensive understanding of the concrete mix ratio and the knowledge to ensure the success of your next construction project.
What is the Concrete Mix Ratio?
The concrete mix ratio refers to the precise proportion of ingredients—cement, aggregates, water, and sometimes additives—used to create concrete with specific properties. This ratio plays a pivotal role in determining the strength, durability, workability, and other essential characteristics of the concrete. Essentially, it acts as the recipe that guides the construction process, ensuring that the resulting structure meets the desired standards and requirements. Without an appropriate mix ratio, concrete may fail to achieve the necessary strength, leading to structural flaws, cracks, or even collapse over time.
Components of Concrete Mix
1. Cement
Cement is a crucial ingredient in concrete, serving as the binder that holds the mixture together. There are various types of cement available, each with unique properties suited for different applications.
Common types
- Ordinary Portland Cement (OPC)
- Portland Pozzolana Cement (PPC)
- Portland Slag Cement
- White Cement
Read our previous article to learn more about types of cement.
Functions of Cement
- Provides cohesion and strength to the concrete mix.
- Initiates the chemical reaction known as hydration, which binds the cement particles with water and aggregates to form a solid matrix.
- Influences the setting and curing time of the concrete.
2. Aggregates
Aggregates are granular materials, including gravel, sand, and crushed stone, that comprise the bulk of concrete mixtures. They contribute to the overall strength, stability, and durability of the concrete.
Common types of aggregates
A. Coarse Aggregates
Typically larger particles such as gravel or crushed stone provide bulk and strength to the concrete mix.
B. Fine Aggregates
Smaller particles such as sand fill the voids between coarse aggregates and help to improve workability and finishability.
Roles of Aggregates
- Provide structural stability and load-bearing capacity to the concrete.
- Reduce shrinkage and cracking by filling voids within the mixture.
- Influence the workability, density, and appearance of the concrete.
3. Water
Water is essential for initiating the hydration process that binds the cement and aggregates together to form concrete. Proper measurement of water is crucial for achieving the desired properties and performance of the concrete mix.
Factors to consider
A. Water-to-Cement Ratio
The ratio of water to cement affects the strength, workability, and durability of the concrete. A higher water-to-cement ratio may increase workability but can compromise strength and durability.
B. Consistency
The consistency of the concrete mix, influenced by the amount of water added, determines its workability and ability to be placed and compacted effectively.
C. Curing
Adequate moisture is necessary for the concrete to cure properly and achieve its desired strength and durability. Proper water management during curing is essential for preventing cracking and ensuring long-term performance.
4. Admixtures
Admixtures are additional substances added to the concrete mix to modify or enhance its properties and performance. They can improve workability, durability, strength, and resistance to adverse conditions.
Common types of admixtures
A. Plasticizers
Also known as water-reducing admixtures, plasticizers improve the workability of the concrete mix by reducing the amount of water required while maintaining consistency.
B. Accelerators
Accelerating admixtures speeds up the setting and curing time of the concrete, allowing for faster construction schedules and early strength development.
C. Retarders
Retarding admixtures delays the setting time of the concrete, useful for hot weather conditions or when extended workability is required.
D. Air-Entraining Agents
Air-entraining admixtures introduce microscopic air bubbles into the concrete mix, improving freeze-thaw resistance and durability in harsh climates.
Types of Concrete
Plain or Ordinary Concrete
Ordinary concrete is the most common type of concrete used in construction. It consists of cement, water, and aggregates (sand, gravel, or crushed stone) mixed. It’s suitable for general construction purposes where high strength is not a primary requirement.
Standard Concrete
Standard concrete is a versatile type used for various applications. It’s a mix of cement, water, and aggregates, with proportions adjusted to achieve desired strength and durability. It’s commonly used in residential, commercial, and infrastructure projects.
High Strength Concrete
High-strength concrete is engineered to have significantly higher compressive strength than standard concrete. It’s achieved through careful selection of materials, precise proportioning, and sometimes the inclusion of admixtures or supplementary cementitious materials. High-strength concrete is used in structures where superior strength and durability are essential, such as high-rise buildings, bridges, and heavy-duty pavements.
Types of Concrete Mix Ratio
Nominal Concrete Mix
Nominal mix concrete refers to concrete mixtures where the proportion of the ingredients like cement, sand, and aggregates are prescribed in terms of volume in a rough manner without considering the properties of individual materials. It’s typically used for small-scale construction works or where quality control is not stringent. The ratios are often denoted in terms of volumes like 1:2:4, which means 1 part of cement, 2 parts of sand, and 4 parts of coarse aggregates.
Standard Concrete Mix
Standard concrete mix is a proportionate blend of specified materials to achieve the desired strength and durability for general construction purposes. Unlike nominal mix, the ratios for standard concrete are precisely calculated based on the properties of the materials used. Common ratios for standard concrete mixes include 1:2:3 (cement:sand:aggregate) for low-strength applications and 1:1.5:3 for higher-strength requirements.
Design Concrete Mix
Design concrete mix involves the detailed calculation and optimization of the concrete mixture to meet specific performance requirements such as strength, workability, durability, and environmental conditions. It considers the properties of individual materials, desired strength, water-cement ratio, admixtures, and other factors to tailor the mix for the intended application. Design concrete mixtures are often used in large-scale construction projects where precise control over concrete properties is crucial.
These different types of concrete mix ratios provide flexibility and control over the quality and performance of concrete in construction projects, ranging from small-scale to large-scale applications.
Concrete Mix Ratio
Type of Concrete | Type of Concrete Mix Ratio | Concrete Grade | Mix Ratio |
Ordinary Concrete | Nominal Concrete Mix | M5 | 1:5:10 |
M7.5 | 1:4:8 | ||
|
| M10 | 1:3:6 |
M15 | 1:2:4 | ||
M20 | 1:1.5:3 | ||
Standard Concrete | Standard Concrete Mix | M25 | 1:1:2 |
M30 | Design Mix | ||
M35 | Design Mix | ||
|
| M40 | Design Mix |
M45 | Design Mix | ||
M50 | Design Mix | ||
High Strength Concrete | Design Concrete Mix | M55 | Design Mix |
|
| M60 | Design Mix |
M65 | Design Mix | ||
M70 | Design Mix |
Factors Influencing Concrete Mix Ratio Decisions
1. Desired Strength
The intended use and load-bearing requirements of the structure dictate the necessary strength of the concrete, influencing the mix ratio selection.
2. Environmental Conditions
Factors like temperature, humidity, and exposure to chemicals or freeze-thaw cycles can affect the performance of concrete, requiring adjustments in the mix ratio.
3. Workability
The ease of placing, compacting, and finishing the concrete, known as workability, is influenced by the mix ratio. A balanced ratio ensures optimal workability without sacrificing strength.
4. Durability
Considerations for long-term durability, such as resistance to cracking, abrasion, and corrosion, guide decisions regarding the mix ratio and the inclusion of additives.
5. Cost and Availability
Availability of materials and budget constraints may impact mix ratio decisions, as certain ingredients may be more expensive or harder to source than others.
6. Desired Finish
The surface appearance and texture desired for the concrete affect the mix ratio selection. Smooth finishes may require a different mix than exposed aggregate or stamped concrete.
Conclusion
Understanding and implementing the right concrete mix ratio are fundamental aspects of construction that cannot be overstated. The mix ratio directly influences the strength, durability, and performance of concrete structures, affecting their ability to withstand loads, environmental conditions, and time. By selecting the appropriate mix ratio based on project requirements, and considering factors such as structural design, environmental conditions, and finish requirements, builders can ensure the longevity and reliability of their constructions. Proper measurement, mixing, and quality control practices are essential to achieving consistent and reliable results. Ultimately, a thorough understanding of concrete mix ratios empowers builders to create durable, resilient, and sustainable structures that stand the test of time.